Saving steps is paying big dividends at ADOT’s vehicle-repair shops
Saving steps is paying big dividends at ADOT’s vehicle-repair shops
At the Tucson shop where the Arizona Department of Transportation repairs and maintains vehicles, technicians once rolled tires across the facility to reach a machine used for repairs.
Today, that machine is located next to the operation’s tire storage, along with the tools and supplies needed for the work. As a result, far fewer steps are required to repair tires.
Technicians once lost time searching various drawers for the right nuts, bolts, fittings and electronic connectors. Today, drawers are color-coded according to items, sizes and uses, better connecting technicians with what they need for a particular repair.
Rather than lugging containers of wiper fluid, technicians now create it by adding tablets with water to a vehicle’s wiper fluid holder. In addition to being a little less expensive, this approach frees space once required to store all of that wiper fluid.
“The littlest details make a big difference,” said Harry Edwards, the foreman.
As ADOT answers Governor Doug Ducey’s call for state agencies to continuously improve all aspects of their operations, employees at the Tucson Equipment Services shop are identifying ways to do their jobs more efficiently, down to how they organize their workstations.
“One of the things we’re challenged to do as employees is look for opportunities to improve upon what we did yesterday,” said Sonya Herrera, director of ADOT’s Administrative Services Division, which includes Equipment Services. “And I think the Tucson shop is a great example of how small changes, when added together, lead to a huge improvement.”
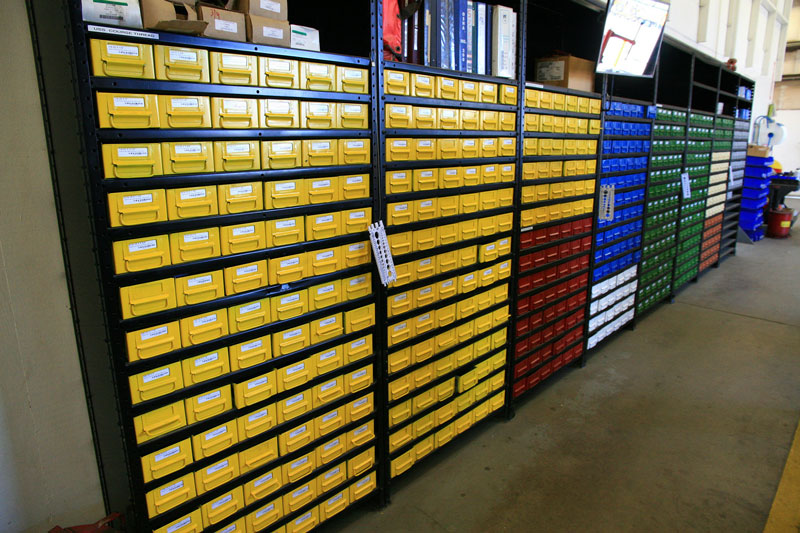
Improvements to date include a tracking system for specialized diagnostic tools that technicians share.
“Rather than spending time looking for it or searching for it, they know exactly who has that tool and can touch base with them to find out when it will be available,” Herrera said.
Devin Darlek, ADOT Equipment Services administrator, notes that applying continuous improvement techniques costs nothing in most cases while producing savings in time and taxpayer money. It’s also spurring a healthy competition among all 23 ADOT Equipment Services shops to identify improvements.
“Process improvements are contagious,” Darlek said. “All employees are excited about this and are working to plug in their own ideas.”
All through the Tucson shop, employees are evaluating processes and procedures to cut down on the steps – and time – needed to perform work. Reducing steps increases the shop’s capacity for other work.
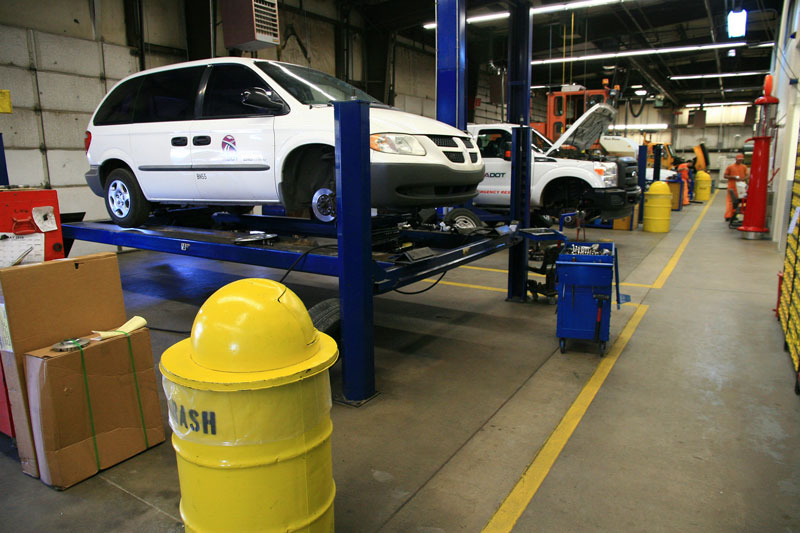
The employees’ review found that mounting and balancing a tire required 277 steps.
Moving the machine in question to where tires are stored, and next to the right supplies and tools, reduced the number of steps required to mount and balance a tire to 28.
Employees saved more steps by taking a close look at each technician’s workspace, and then reorganizing – rebuilding workbenches in some cases – to focus on the tasks each person performs most often as well as ergonomics.
After employees assessed which items in the parts area were in highest demand, Kevin Potts, the facility’s equipment parts supervisor, moved those items closer to the entrance. Where it once took 10 steps to dispense one of the faster-moving parts, it now takes just three.
That improvement also has reduced inventory, which in turn reduces overhead costs, and made accounting for inventory much more efficient.
“Instead of having three months of inventory sitting on my shelf, I’ve got just two or three weeks of inventory sitting on my shelf because I have really good vendors 20 minutes away,” Potts said.
Technician Shane Blasdel said the many improvements to date at the Tucson shop offer benefits beyond saving steps.
“Shop’s a lot cleaner, a lot more efficient, a lot safer,” Blasdel said.
Because continuous improvement is, by definition, continuous, accomplishments to date are just a start.
“No idea’s too small,” said Edwards, the Tucson shop foreman.